Our Factory
McConnel Power Arms are precision-engineered at the company's production facility in Ludlow, Shropshire, where the machines are designed, built and tested.
The vast majority of components are created in-house and every single machine is subjected to a rigorous testing programme before being released to customers.
Here's how our dedicated team transform sheets of raw steel into the award-winning Power Arms popular all over the world.
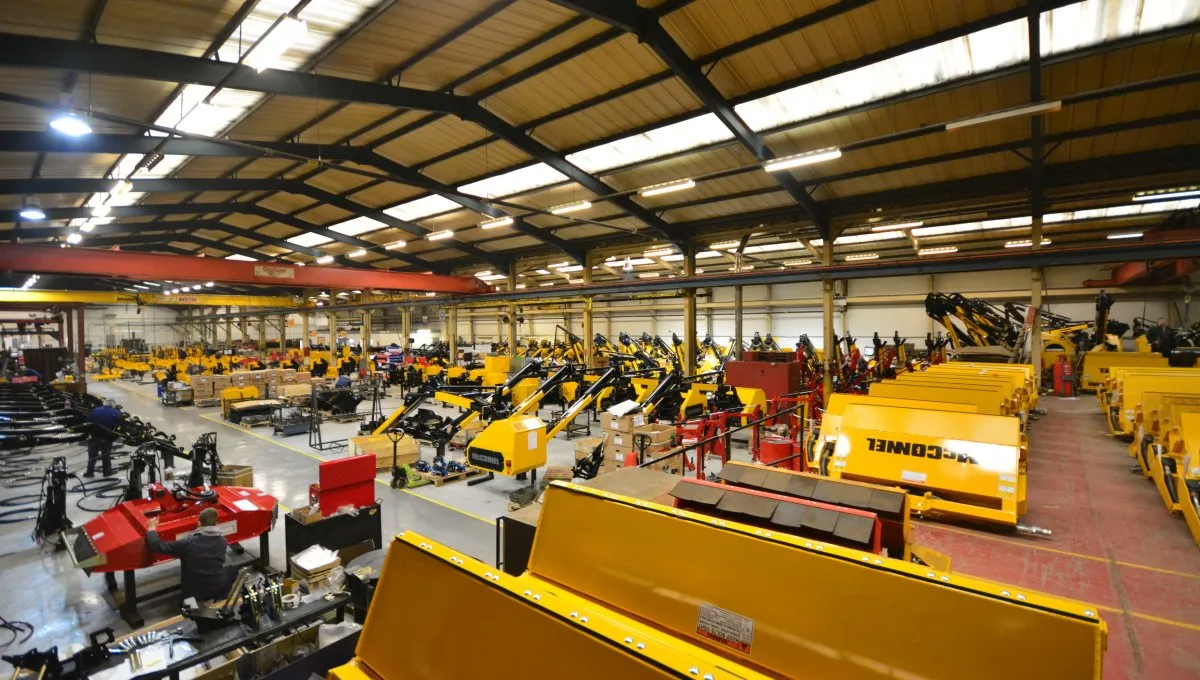
Components
More than 10,000 components-a-week are created from steel plate ranging in thickness from 1.6mm to 65mm. The process consumes up to 65 tonnes of steel.
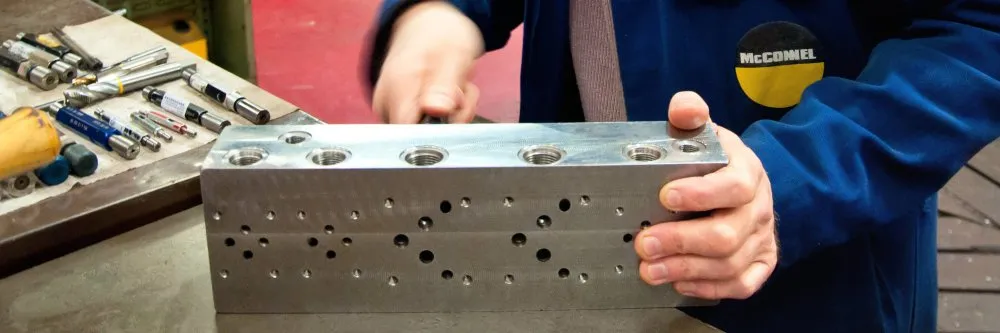